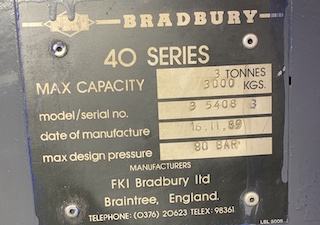
|
When I decided to have ago at changing the piston seals on my fairly old Bradbury 40 lift, I could not find anything on the internet to help me, so I thought I would try and make a few notes and put this on my obscure website so that if Google finds it, it may be of some help to someone doing this job to their lift in the future.
|
|
Firstly, I decided I needed to change the seals when puddles of oil started appearing at the foot of the column containing the hydraulic ram. It was fairly easy to buy new seals thanks to eBay and I must say the seller was very helpful insomuch as a quick chat over the phone gave me an idea of what to do. This may be stating the obvious, but the seals are on the piston at the bottom, so the whole thing needs to come out to get to them. This part of the piston is of a wider diameter than the piston you see exposed in the raised position. The first thing to do is to move the ramp to a mid-way position and support it. I actually have a 2-post ramp installed in the same place as the Bradbury, so I used that to support the ramp. It was suggested to me, supporting it on 4 oil barrels would be a good solution otherwise.
|
|
Photo: old flat seal
Once the weight is taken, you can undo the connection at the top between the piston and the stirrups that are connected to the ramp. The next thing to do is to pump out the piston by using the up control as you would do normally when moving the ramp upwards. You will need secure footing to be able to guide out and pull out the piston once it gets to its full height. An assistant may be a good idea to operate the controls. There is probably a plastic collar to remove at the top of the ram. I could not initially get the piston to come out and I also had an issue with height, but as it was up against a pitched roof, I loosened off the ground anchors and used a crow bar to tilt the column in very slightly, enough to gain more head room.
|
|
Photo: new seal
I then used the crowbar to lever between the latching profile on the piston (the piston should rotate) and the top of the column. It then did not take much to withdraw it. It is quite heavy and you are working at height, so this could potentially be quite tricky. With it removed and on axle stands it was very obvious that the seal had flattened out over time. My seal kit contained the orange seal support, but not the white piece so that was reused. I used red rubber grease (for no good reason other than I had some) to grease up the new seal.
|
|
Photo: Top end of cylinder with piston removed.
To reassemble, the first thing to do is to get the piston back into the cylinder. This was not too difficult, but again you are working at height doing this.
|
|
Photo: new seal with red rubber grease
The next thing to do is to drain the hydraulic oil out of the cylinder, or at least drop the level of it, as you will not be able to push the piston down against the oil. I cannot quite remember how I did this, but I think I removed the oil reservoir and may be just operated the down lever. Either way, I removed some oil somehow. The piston needs to be persuaded to lower into the cylinder until its lower enough to reconnect to the ramp stirrups. After that the weight of the ramp will do the job.
At this point, put some fresh hydraulic oil in and operate the ramp up and down a couple of times, so the system self-bleeds and you should be good to go.
|